The sound you hear from a speaker is mainly produced from the vibrations of the speaker cone. There’s a lot of science involved in how a cone works. There’re different materials used in making speaker cones. These materials include paper, plastic, fabric, and metal. Each cone material has a certain impact on the performance of a speaker. There’s an unending debate on which cone material performs the best. There’re certain characteristics that make one material more ideal than the other. Let’s have a look at the major cone materials used in making speaker diaphragms in order to understand how they work and their impact on speaker performance.
1. Paper cones
Paper is a material that is affordable and readily available. Most of the older types of speakers were made of paper cones. Paper is a lightweight material and is able to follow the motions that are generated by the coil. Paper material is cheap, especially when making large speaker cones. However, paper absorbs moisture and this increases its mass while altering its damping characteristics. Also, paper cones tear easily from stress. They puncture easily.
Basically, paper cones are made of a formulation of various materials, especially a combination of wood, wool, and felt. The paper formulations are also mixed with various chemicals to make them more durable and ideal for making speaker cones. As such, paper cones can be made of different combinations depending on the manufacturer’s design.
Paper speaker cones are either pressed or non-pressed during the manufacturing processes. Non-pressed cones offer a larger surface area such that they push more air, thereby delivering louder sound. Non-pressed paper cones also have higher sensitivity such that they are more power-efficient. However, non-pressed paper is stiffer as a result of chemical treatment. On the other hand, pressed paper cones to have a smaller surface area but boast of having fewer quality issues than non-pressed paper cones.
2. Plastic cones
Plastic cones are another form of cone material. Plastic is preferred over paper for its more rigid and durable. There’re different forms of plastic used in making cones. Early speaker manufacturers used a form of plastic known as polystyrene to make cones in flat-panel speakers. Although polystyrene is rigid and light, it becomes noisy when flexing, thereby its use was limited. Today, the most common form of plastic used in making cones is known as polypropylene. Polypropylene has low distortion and doesn’t absorb moisture. As such, it’s commonly used in bathroom speakers, in-wall and ceiling speakers, and home theatre speakers.
Polypropylene has great characteristics that make it ideal for making most cones. For instance, it’s strong, stable, consistent, and well-damped. Moreover, polypropylene is flexible and easy to work with during the manufacturing process. It resists mold and mildew for it is moisture resistant. As such, it’s more durable than paper cones.
Polypropylene is also preferred over other forms of plastic for its being lightweight. As such, it moves easily according to the coil vibrations. Moreover, it has electronic insulation properties. It doesn’t allow current to flow to other speaker areas. However, a major shortcoming of polypropylene is that it’s noisy when flexed.
3. Metal cones
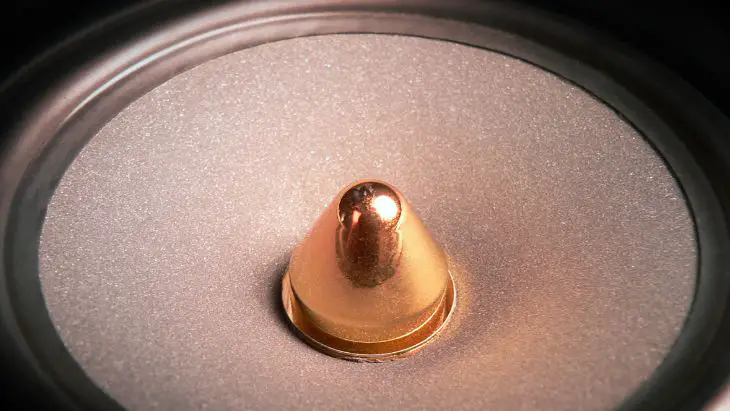
Certain metals are used in making speaker diaphragms, with the most common ones being aluminum and magnesium. Metal boasts of having the least coloration and distortion when compared to other materials. However, metal exhibits poor damping properties. Aluminum is often used for woofer cones. Magnesium is lighter than aluminum but both share similar stiffness and strength. Magnesium has poorer damping properties than aluminum. On a similar note, aluminum is relatively affordable and easy to work with.
While metal cones are extremely stiff and durable, they have the disadvantage of flexing and ringing. Ringing destroys the quality of sound. While metal can be doped with chemicals to enhance its damping properties, doing so increases its mass and this brings about performance issues.
4. Fiber cones
Carbon fiber and Kevlar are some of the most common fiber materials used in making cones. Carbon fiber is mostly used in woofer drivers. It’s lightweight and durable. Moreover, it’s tough and flexible, thereby attaining high output. Carbon fiber, however, is mostly used as part of composite materials in a formed or woven state. It’s also used as a covering material over paper cones to enhance the strength of paper. Carbon fiber is hard to work with. Thus, it’s widely used as a composite material rather than a plain material.
Kevlar is an artificial fiber material. It’s popular for making bulletproof vests. Kevlar is also used in making speaker diaphragms. It’s typically woven and formed when making cones. Kevlar can be used to make cones as a plain material or it can be coated with other materials. Although Kevlar has great properties like being rigid and lightweight, it has the shortcoming of ringing like a bell due to limited dampening properties. As such, it’s unable to dampen some resonances. Therefore, it’s often used with other materials as composites for better results.
5. Woven composite cones
Speaker manufacturers are always trying to come up with the best cone material. Innovations have led to the development of woven composites to make better cones. There’re many techniques used in making woven cones. Woven cones mostly comprise glass, carbon fiber, and aramids. Some woven sheets are resin treated whereas others are not.
Most woven fibers are lightweight and stiff, making them ideal for cones. However, when woven fibers are coated with epoxy seals, they become heavy, thereby proving less ideal than paper and plastic cones. As such, some woven fibers are sealed with polypropylene to maintain their lightweight property. Woven fibers are usually expensive and not readily available like paper and polypropylene, making them less ideal for mass production.
In conclusion, what’s the best cone material?
The best cone material is a material that doesn’t flex. It should have the best pistonic motion. In addition, the best material is the one that is well dampened, lightweight, and rigid. It should be able to start or stop vibrating as soon as needed. The goal is to use a material that can reproduce sound signals as accurately as possible with reduced distortion. However, there’s no single perfect material. For instance, the best material should be lightweight and rigid, but more rigid materials have more mass, and materials with lower mass are less rigid Also, some materials are best for making low-frequency drivers and others are best for making high-frequency drivers. No single material is perfect for making both low and high-frequency drivers. Thus, designers select materials that are close to perfect but with minimal shortcomings for specific applications.
Basically, the main goal when choosing a speaker cone material is a material that reproduces voice coil signals in the most accurate way and with minimal distortion. As such, the best material is one that maintains tight movement and maximizes the point at which frequency breakup occurs. Thus, manufacturers continue exploring many possibilities for combing all the desirable properties by making cones with composite materials.
Michael Evanchuk is a San Francisco-based sound engineer with 20 years’ experience installing, troubleshooting, and repairing commercial, automotive, and household sound equipment. Evanchuk owns an auto stereo center, where he offers highly competitive car audio installation and repair services. He has written dozens of articles on different sound engineering topics, all of which have been published in leading journals, blogs, and websites.